History
The origin of Kong began a long time ago, in 1830 in a workshop at the foot of the Alps where Giuseppe Bonaiti gave rise to our story, writing important pages for Made in Italy. The care to provide maximum protection for human lives, together with the dreams that men will “hang” while climbing peaks, led Bonaiti to export his products and philosophy throughout the world. His carabiners have become a real fixture for everyone who practices vertical disciplines.
In 1977, the Bonaiti company changed its name to Kong, but its mission remains the same.
“To manufacture safety where risk is the protagonist”
The entire production cycle, from design to packaging, is made in our factory of 10,000 square meters, located in Monte Marenzo (LC), Italy, where each item of Personal Protective Equipment (PPE) is tested piece by piece and then sold throughout the world. We can proudly say that, first of all, we are “manufacturers”.
• Our 80 employees perform their daily activities with passion to produce high quality systems that ensure maximum safety.
• Our robots test 100% of our items at 70% of their breaking load.
• Our operators check 100% of the appearance and functionality of our products.
“KONG, from the past to the future, the evolution of safety”
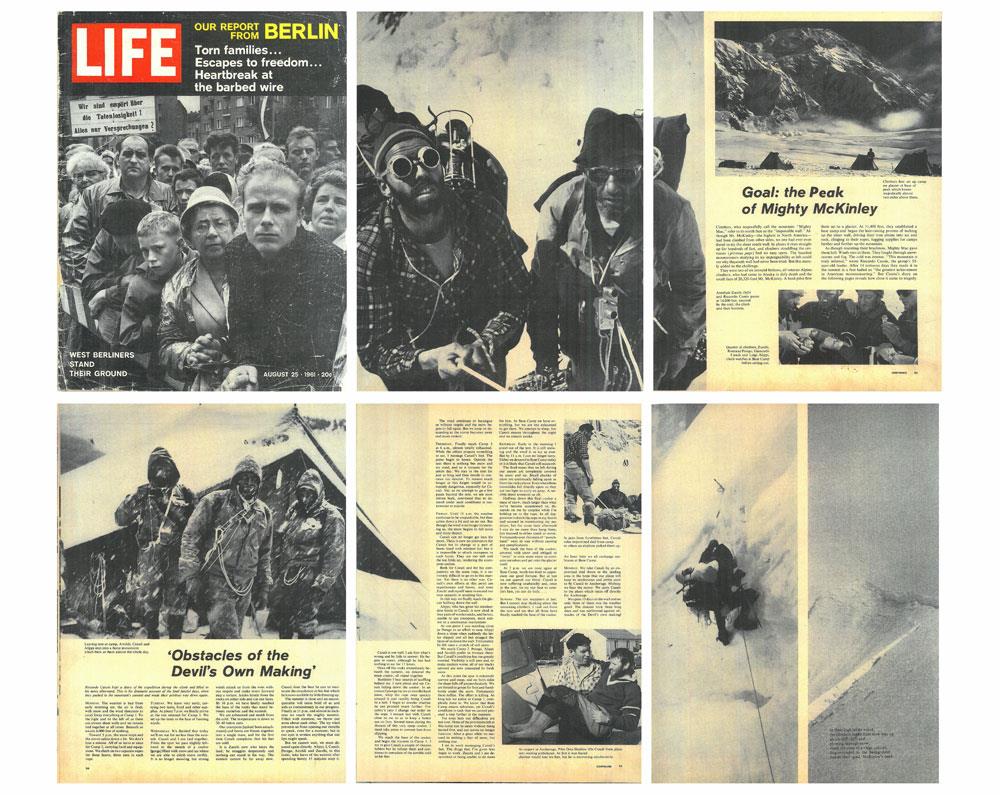
THE BIRTH OF MOUNTAINEERING
Mountaineering became a sports discipline in the second half of the nineteenth century, when the most difficult summits were conquered; even those hitherto considered impossible. The first mountaineering manuals described the equipment that climbers should carry with them to face the climb safely. The use of carabiners to overcome the difficulties of ascents dates back to 1914, when O. Herzog, and his brother Willi, climbed the south face of Schüsselkarspitze, with the aid of pear-shaped hooks used by firemen in Munich.
In the domestic market the Bonaiti company was the only one to produce a specific carabiner for mountaineering. The technical and practical advice of R. Cassin was instrumental in improving the D-shaped carabiner for sale in Europe, and the name of the famous mountaineer made the Bonaiti name well-known to foreign importers of mountain equipment. National distribution was ensured by the same representatives that dealt with buckle products, who sold the product to hardware stores.
In the 1960s the first light alloy carabiners for extreme mountaineering were manufactured, and this new material reduced the product’s weight from 200 to 65 grams. These carabiners were highly appreciated by rock climbers due to aesthetic matters, since the different colours, obtained through an anodising process, linked to the rest of their equipment.
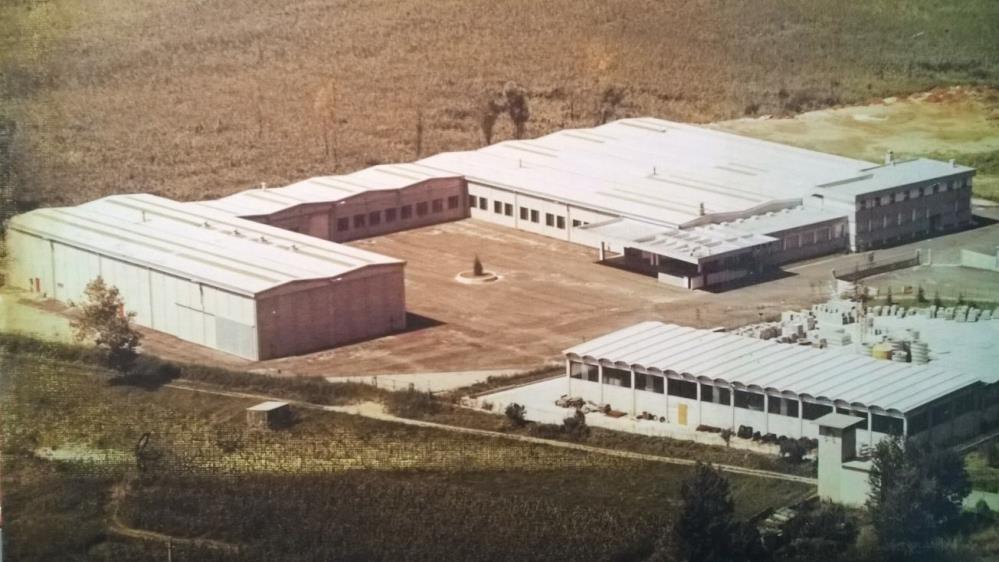
THE BIRTH OF KONG
The growing demand for carabiners, together with the issues of interior space, drove the management to decentralise certain processing stages.
In the 1970s, the department that produced carabiners, which was confined in a small space, needed a larger area for the cohesiveness of operations, and for its development. The warehouses of Giuseppe e Fratelli Bonaiti could not be extended due to the administrative constraints imposed by the Regulatory Plan of Calolzio. In 1977 the company purchased a plot covering 30000 m2 in Monte Marenzo, so that they could build a new production site, to which they would transfer the manufacture of carabiners.
1977, right here in Monte Marenzo, saw the launch of Kong S.p.a., the only production plant where still today over 3000 products are distributed and sold all over the world.
In order to create a corporate image that was recognisable in the countries to which it exported its goods, in 1982 the company registered the name and trademark Kong in various countries: the current and well-known oval that recalls the outline of a carabiner.
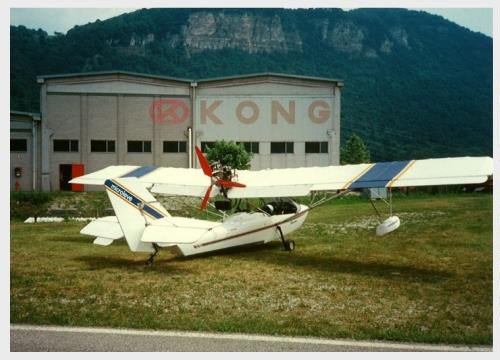
INTERESTING FACTS
In 1978 the gravel that was used during the construction of the new factory to settle marshland, was massed downstream of the factory to create a dynamic push that would balance the structure of the buildings.
In 1986, this 300-metre long embankment was paved, and legalised as a non-sloping airfield, recognised by the A.N.P.S. (Associazione Nazionale della Polizia di Stato - National Police Association), as a section of Malpensa airport.
Today this runway is also used by the Civil Defence and Mountain Rescue helicopters for exercises in lowering and recovery using stretchers.
Currently, in addition to the Volo Club Lecco Kong, with about fifty members and around twenty aircraft, there is the very active Pilota per Sempre flying school which trains a few dozen new ultralight pilots every year.
Since 2017 it has also been home to the first Italian school of ENAC certified drones.
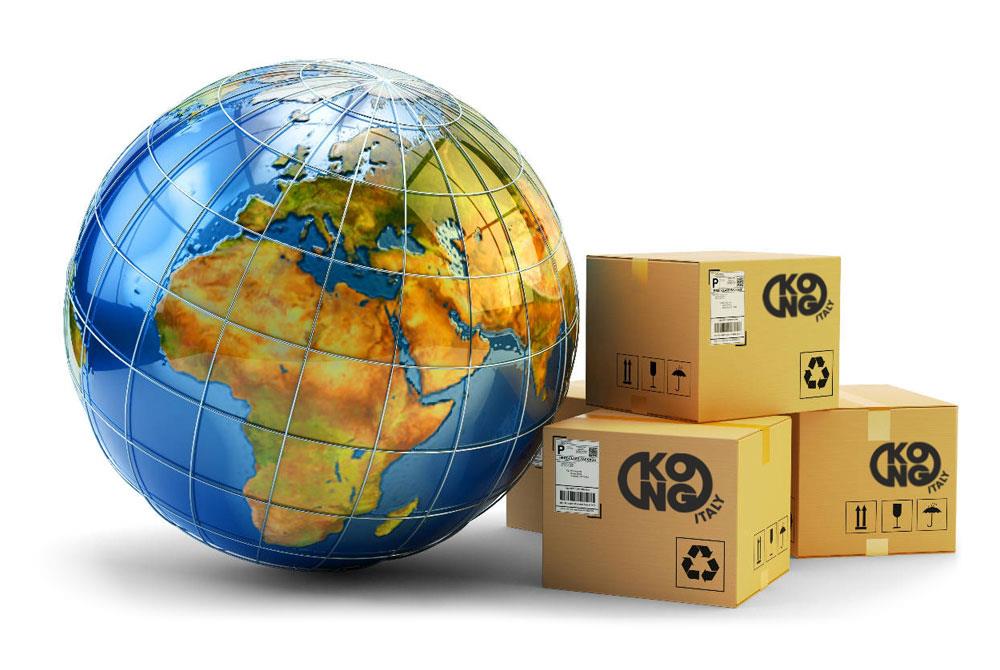
COMMERCIAL DECENTRALISATION IN STRATEGIC COUNTRIES
From the early ‘90s Kong began to set up companies with commercial and non-productive objectives in emerging countries. This was in order to have control and a direct presence in countries that were beginning to offer some very interesting developments and opportunities.
Kong Deutschland (1992), Kong Russia (2007), Kong USA (2009), Kong America Do Sul (2013) and the latest Kong Far East (2017) are realities that within a few years led Kong to have a global approach, with the dynamics of a "multinational".
There still remains only one production site, that of Monte Marenzo in Italy, which in a covered area of 10,000 m² employs about 80 people, including labourers, planners, designers, administrative staff and salespeople.
The role carried out by the planners and designers is particularly important; they carefully analyse, interpret and anticipate market needs.
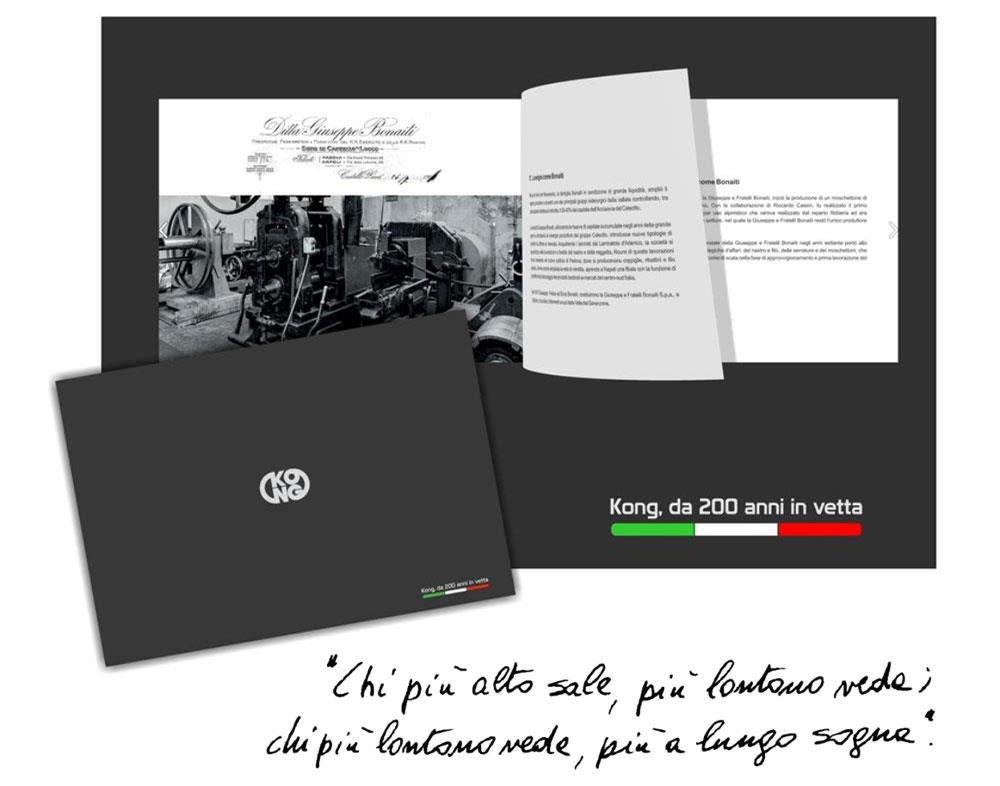
DOWNLOAD "KONG, 200 YEARS AT THE TOP"
The economic crisis of 2009 crippled many national entrepreneurial companies, and also the rich territory of Lecco suffered greatly. Kong coped with the harsh blow with a number of notable business choices, especially the choice to internalise some processes previously contracted to external companies.
A new textile department, new machinery, training centre, and new sales offices gave work to internal staff, avoiding retrenchment of employees.
Today, after almost ten years, we can look back on a situation of steady growth, both in terms of turnover and the number of new recruits.
A mountaineering approach has always been part of the company’s philosophy, even in terms of business development; a slow but steady climb, which for nearly two hundred years has led Kong to the summit.
As Marco Bonaiti wrote in an old catalogue:
“The higher you go, the wider you see; the wider you see, the longer you dream”